Уральские роботы заменят людей на опасных участках производства
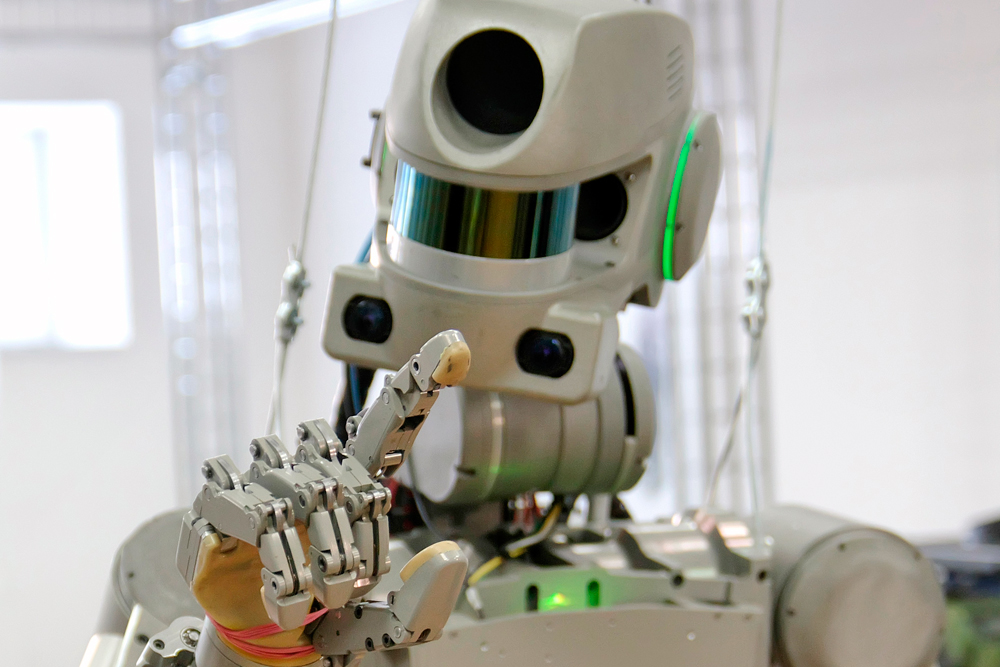
Более 80 единиц автоматизированного оборудования оказались высокоточными роботизированными комплексами, такими сегодня экипируют производственные линии на ведущих предприятиях Японии, Германии, Италии и Южной Кореи. Но особый интерес вызвала умная установка лазерной наплавки для упрочнения деталей электромашин, которая оказалась отечественной разработкой, не имеющей аналогов в мире.
Вместе с тем подобные разработки с успехом ведутся в Челябинске и Магнитогорске. Промышленные роботизированные системы востребованы и успешно внедряется на многих предприятиях региона и за его пределами. Правда, далеко не в той мере, в которой это требуется для научно-технологического прорыва.
"В основополагающем документе "Стратегии научно-технологического развития Российской Федерации", утвержденном указом президента в декабре 2016 года, переход к роботизированным производственным системам обозначен в числе главных приоритетов развития", - сообщил гендиректор челябинской компании-разработчика роботизированных систем "Альфа-Интех", член правления Национальной ассоциации участников рынка робототехники (НАУРР) Анатолий Перепелица.
Однако в 2017 году на предприятиях страны было установлено чуть более 700 роботов, а в 2018 году - 860. В итоге сегодня на 10 тысяч работников у нас приходится не более четырех роботизированных комплексов. При этом плотность роботизации в мире составляет около 70 единиц на 10 тысяч человек. В Японии и Германии - это 300 единиц, а в Южной Корее - 630, сообщил эксперт.
По данным Центра экономических показателей при Лондонской школе экономики в развитых странах до 10 процентов прироста ВВП за последние годы обусловлено именно внедрением промышленной робототехники. У нас тот же вклад в прирост ВВП оценивается в скромные 0,1 процента.
При сравнительно небольших объемах внедрения промышленных роботов отечественные компании-разработчики вынуждены собирать заказы по всей стране. Компания Перепелицы сотрудничает с предприятиями "Росатома", "Роскосмоса" Липецким и Магнитогорским металлургическими комбинатами. К примеру, по заказу ММК разработала систему для агрегатов непрерывного горячего цинкования, где робот помогает снять с металлического листа шлаковый слой в ванне с расплавленным цинком. Раньше эту рискованную работу выполняли люди, а теперь подобные устройства планируется установить на всех агрегатах непрерывного горячего цинкования.
В МГТУ имени Г.И. Носова тоже помогли градообразующему комбинату - создали уникальную систему автоматического управления электрическими режимами дуговых сталеплавильных печей и установок "печь-ковш", получившей название "Радуга".
"Ее применение в электросталеплавильном цехе ММК позволило повысить скорость нагрева металла и обеспечить существенный технический и экономический эффект, в десятки миллионов рублей в год только для одного агрегата", - пояснил заведующий кафедрой автоматизированного электропривода и мехатроники МГТУ Александр Николаев.
Кроме того, кафедра проводит исследования по эксплуатации промышленных кранов, где роботизированный комплекс обеспечит так называемую функцию "антираскачивания" грузов. Представьте ковш с раскаленным металлом. При движении металл может выплеснуться, а разработка обеспечивает оптимальную траекторию, избавляющую от этого риска. Другими словами, если раньше некоторые операции нельзя было проводить на высоких скоростях, то теперь это будет возможно. Кстати, уже оформляется грант на внедрение этого ноу-хау.
"Уральский инжиниринговый центр" работает с ММК, группой ЧТПЗ, компанией "Мечел", ЧЭМК и ЕВРАЗ НТМК - наиболее крупными предприятиями, способными внедрять наилучшие из доступных технологий. Для последнего, к примеру, модернизировала роботизированную прессопрокатную линию колес, что, по словам президента холдинга, члена-корреспондента РАЕН Валерия Бодрова, позволило добиться стабильной точности позиционирования заготовки плюс-минус 1 миллиметр, тем самым уменьшить ее вес и снизить затраты на последующую механическую обработку. А производительность линии после модернизации выросла на 15 процентов.
По сути, роботизированные комплексы оказываются хорошим подспорьем там, где нужно снизить риск влияния "человеческого фактора" - на вредном производстве, где речь идет о тяжелых условиях труда, при монотонном технологическом процессе, когда одну и ту же нехитрую операцию требуется повторить несколько тысяч раз. Или как раз наоборот, где речь идет об одной, но сложной операции, которую нужно провести с максимальной точностью, поскольку цена ошибки очень велика. Однако, как показывает практика, предприятия идут на вложение в модернизацию техпроцессов, когда экономический эффект измеряется конкретной выгодой рублем. И окупаемость не превышает двух-трех лет.
При этом эксперты отмечают, что основными игроками рынка робототехники сегодня остаются зарубежные компании-производители промышленных роботов. А вклад отечественных интеграторов, разрабатывающих собственные и модернизирующих импортные РТК, пока невелик. К примеру, "Альфа-Интех" выполняет 11-12 заказов в год. И при всей наукоемкости этой работы, могла бы производить гораздо больше. Но как говорится, каков рынок, таковы и игроки.
"Возможно, развитие промышленной робототехники могло бы ускорить создание государственного органа, уполномоченного решать эту проблему, - считает Анатолий Перепелица. - К сожалению, в России пока нет собственной национальной программы внедрения РТК или хотя бы скромных подпрограмм. Более того, в программе "Цифровая экономика РФ", которая, по логике, должна была конкретизировать утвержденную президентом "Стратегию научно-технологического развития", среди перечня технологий робототехника вообще отсутствует, а есть лишь скромные "компоненты робототехники и сенсорика". Вероятно, следует исправить этот казус"?
Робот-спасатель "Федор", разработанный по заказу МЧС НПО "Андроидная техника" и Фонда перспективных исследований, в августе поработал на Международной космической станции в условиях невесомости, высокого уровня излучения и перепадов температур. "Федор" соединял и разъединял электрические разъемы, общался с космонавтами и даже отвечал на вопросы. Сегодня подобных испытаний антропоморфных роботов еще не проводилось. Со временем планируется освоить технологию, при которой космонавту не нужно будет выходить в открытый космос. Непосредственную работу за пределами станции за него выполнит управляемый робот.